Business Development
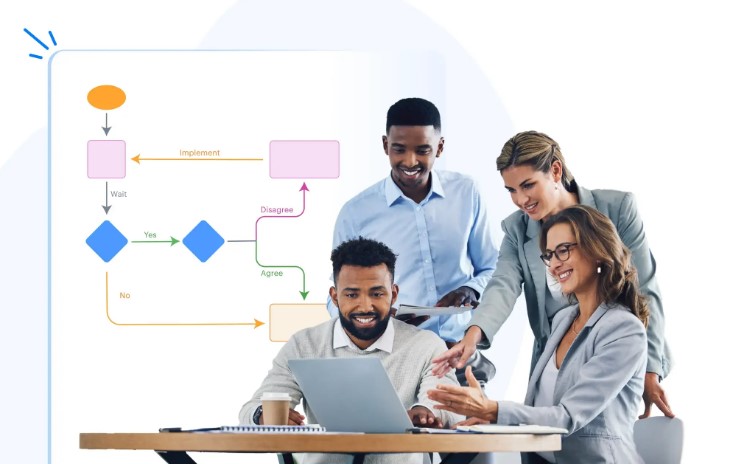
Optimization of Internal Processes
Optimizing internal processes refers to a set of actions aimed at improving efficiency, reducing costs, increasing quality, and enhancing the overall performance of an organization. These actions involve detailed analysis of processes, identifying weaknesses, and implementing changes for continuous improvement. Below is a comprehensive explanation of this concept:
- Definition and Importance of Process Optimization
a) Definition:
Process optimization involves reviewing and refining work processes to increase productivity and effectiveness. This includes reducing waste, improving scheduling, and optimizing resource use.
b) Importance:
Optimizing processes helps organizations stay competitive in the market by reducing costs and improving quality. Additionally, these actions can lead to improved employee and customer satisfaction. - Stages of Process Optimization
a) Identifying Key Processes:
In this stage, organizations must identify the key and critical processes that have a direct impact on overall performance. These processes usually include production, distribution, sales, and after-sales services.
b) Analyzing Processes:
Once the key processes are identified, the analysis phase begins. This involves a detailed review of each step in the process, identifying bottlenecks and weaknesses, and gathering related data.
c) Redesigning Processes:
Based on the results of the analysis, existing processes are reviewed and redesigned. The goal is to simplify processes, eliminate unnecessary activities, and increase efficiency.
d) Implementing Changes:
The proposed changes must be carefully implemented. This phase includes staff training, changes in systems and tools, and managing organizational changes.
e) Monitoring and Evaluation:
After implementing the changes, continuous monitoring of process performance is necessary. Ongoing evaluation of results helps ensure the organization has achieved its optimization goals. - Methods and Techniques for Optimization
a) Business Process Analysis (BPA):
This technique involves analyzing processes to identify improvement opportunities and provide practical solutions.
b) Six Sigma:
A systematic approach for improving process quality by reducing variability and eliminating errors. This method uses statistical tools to measure and enhance process performance.
c) Lean Management:
Lean management focuses on eliminating waste and unnecessary activities to create more value for customers and improve efficiency.
d) Process Automation:
Using modern technologies to automate processes can help reduce errors, increase speed, and reduce costs. - Benefits of Process Optimization
a) Cost Reduction:
By eliminating waste and increasing efficiency, organizations can reduce operational costs.
b) Quality Improvement:
Process optimization can lead to better quality products and services, which ultimately increases customer satisfaction.
c) Increased Productivity:
Improved processes allow employees to perform their tasks more efficiently, leading to higher overall productivity.
d) Greater Flexibility:
Organizations with optimized processes can respond more quickly to market changes and customer needs. - Challenges in Process Optimization
a) Resistance to Change:
One of the biggest challenges in process optimization is resistance from employees and managers to changes. For success, an appropriate organizational culture needs to be fostered.
b) Initial Costs:
Process optimization may require significant initial investment, including purchasing new equipment, upgrading technology, and training employees.
c) Process Complexity:
Some processes may be very complex, and optimizing them might require a lot of time and resources. - Success Strategies in Process Optimization
a) Senior Management Support:
Support and commitment from senior management is essential for successful process optimization. This support should include providing resources, offering a clear vision, and backing changes.
b) Employee Involvement:
Involving employees in all stages of optimization, from identifying problems to implementing changes, can help reduce resistance and increase the success of the project.
c) Using Technology:
Using modern technologies such as process management software, data analysis tools, and automation can greatly assist in process optimization.
d) Focusing on Continuous Improvement:
Process optimization should not be a one-time activity. Organizations should view continuous improvement as part of their organizational culture, regularly evaluating and refining their processes.
Conclusion
Internal process optimization is a vital strategy for organizations seeking to increase efficiency, reduce costs, and improve quality. By applying the right techniques, managing changes effectively, and focusing on continuous improvement, organizations can achieve significant benefits and perform more successfully in today’s competitive environment.
L-mohammadi
0
Tags :